Alcast Company Things To Know Before You Buy
Alcast Company Things To Know Before You Buy
Blog Article
Some Ideas on Alcast Company You Should Know
Table of ContentsAlcast Company Fundamentals ExplainedThe Alcast Company DiariesSome Known Details About Alcast Company The Facts About Alcast Company Revealed4 Simple Techniques For Alcast CompanySee This Report on Alcast CompanyExcitement About Alcast CompanyLittle Known Facts About Alcast Company.
It had excellent strength and machinability. There are many various other aluminum alloys that can be utilized for casting parts. To figure out which alloys would be excellent for your tasks, call Impro.
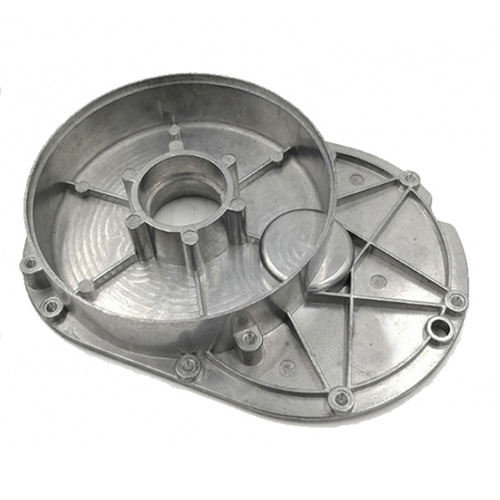
(AA), based in North America, has produced specs that regulate light weight aluminum alloys' make-up, properties, and classification. There are 2 kinds of aluminum alloys wrought and cast.
An Unbiased View of Alcast Company
Cast aluminum alloys are made by melting pure light weight aluminum and combining it with other steels while in fluid form. After that the mix is poured into a sand, pass away, or investment mold. After solidification, the metal is eliminated from its mold. At this stage, it is in either its final form or as a billet or ingot for further processing.
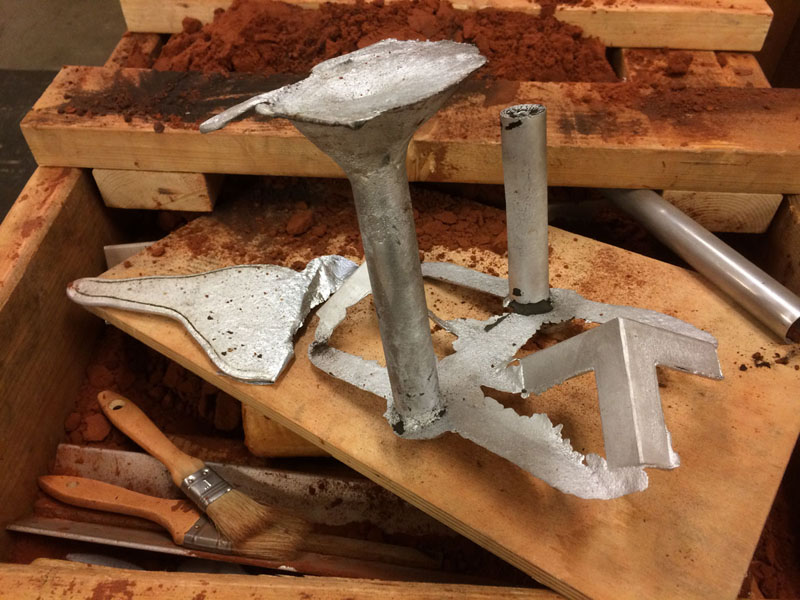
There are many small differences in between functioned and cast aluminum alloys, such as that actors alloys can include more considerable amounts of various other steels than wrought alloys. However the most significant distinction in between these alloys is the manufacture process via which they will go to deliver the end product (aluminum casting manufacturer). Apart from some surface treatments, cast alloys will certainly leave their mold and mildew in almost the specific solid form desired, whereas wrought alloys will certainly undergo several adjustments while in their solid state
The 9-Second Trick For Alcast Company
If you think that a functioned alloy might be the very best for your project, have a look at a few of our articles that describe even more concerning certain wrought alloys, such as Alloy 6061 and Alloy 6063. On the other hand, if you think an actors alloy would be better for you, you can discover more about some actors alloys in our Alloy 380 and Alloy 383 short articles (coming soon).
When picking a light weight aluminum foundry for your manufacturing needs, it's crucial to research a number of factors. Among the most crucial elements to take into consideration is the experience and proficiency of the factory. Selecting a shop that has the right knowledge of the light weight aluminum spreading process, and the portfolio to show for it, assists to have an effective end result for your task.
All About Alcast Company
Having the experience and industry expertise to engineer your spreadings for optimal production and quality results will improve the task. Making aluminum spreading needs a complex set of procedures to attain the appropriate outcomes. When choosing a brand-new aluminum foundry to companion with, guarantee they have comprehensive industry experience and are knowledgeable concerning all facets of the aluminum casting procedure: style, production, product analysis, and item screening.
The foundry should likewise have a proven performance history of supplying phenomenal products that meet or go beyond customer assumptions. Quality control should likewise go to the top of Find Out More your listing when choosing a light weight aluminum factory. By dealing with a qualified foundry that follows the standards for quality control, you can protect the stability of your product and ensure it fulfills your requirements.
The Best Strategy To Use For Alcast Company
By choosing a business that supplies solutions that meet or exceed your product requirements, you can be sure that your job will certainly be finished with the utmost accuracy and efficiency. Specific light weight aluminum shops specialize in specific sorts of manufacturing processes or casting methods. Various components call for various production methods to cast aluminum, such as sand spreading or pass away casting.
Pass away spreading is the name offered to the process of developing intricate steel components through use molds of the component, additionally called dies. The process makes use of non-ferrous steels which do not include iron, such as aluminum, zinc and magnesium, as a result of the desirable buildings of the steels such as low weight, greater conductivity, non-magnetic conductivity and resistance to rust.
Die spreading manufacturing is fast, making high manufacturing degrees of components very easy. It creates more parts than any type of other procedure, with a high degree of precision and repeatability. To get more information about die spreading and die spreading materials made use of while doing so, continued reading. There are 3 sub-processes that fall under the classification of die casting: gravity pass away casting (or permanent mold casting), low-pressure die casting and high-pressure die casting.
The smart Trick of Alcast Company That Nobody is Discussing

The pure steel, also known as ingot, is included in the heating system and maintained the molten temperature of the metal, which is then transferred to the injection chamber and infused into the die. The stress is then kept as the metal strengthens. Once the metal solidifies, the cooling process begins.
The thicker the wall surface of the component, the longer the cooling time as a result of the amount of interior metal that additionally needs to cool. After the component is fully cooled, the die cuts in half open and an ejection system pushes the part out. Following the ejection, the die is closed for the following injection cycle.
Alcast Company Fundamentals Explained
The flash is the extra product that is cast throughout the procedure. This have to be cut off making use of a trim device to leave simply the major part. Deburring eliminates the smaller sized pieces, called burrs, after the cutting procedure. The element is brightened, or burnished, to offer it a smooth coating.
Today, top manufacturers utilize x-ray testing to see the entire inside of components without reducing into them. To get to the ended up product, there are 3 primary alloys made use of as die casting product to choose from: zinc, aluminum and magnesium.
Zinc is one of the most secondhand alloys for die spreading due to its lower cost of raw products. Its corrosion resistance likewise enables the parts to be lengthy long-term, and it is one of the more castable alloys due to its lower melting point.
Alcast Company for Dummies
As pointed out, this alloy is among the most frequently utilized, yet makes will, sometimes, select aluminum over zinc due to aluminum's manufacturing benefits. Light weight aluminum is very affordable and among the much more versatile alloys. Light weight aluminum is made use of for a variety of different items and markets anything from home window structures to aerospace products.
Report this page